Ceramic filters for base stations of the 5G
Shimadzu’s technology to support the research and production of ceramic filters and conductive silver paste for base stations with the advent of the 5G era
Background introduction
5G technology refers to fifth-generation mobile communication technology. Compared to 4G technology, it has the characteristics of high transmission rate, low latency, and large network capacity. At the same time, the 5G signal frequency band is high, the penetration capability is poor, the transmission distance is short, and the coverage capability is weak. As a result, the number of 5G base stations will be much higher than for 4G, and construction of early 5G architecture will focus on these base stations. For example, the Chinese government's infrastructure development policy, "New Construction," was led by three major telecommunications carriers that installed over 700,000 5G base stations in 2020.
The design of 5G base station antennas has been integrated, radio frequency components used for signal processing have been significantly modified, and the number of antenna filters have increased. Therefore, ceramic dielectric filters with light weight and small volumes have been adopted, and it is likely that they will gradually replace the existing metal cavity filters.
Manufacturing process of ceramic dielectric filters:

Technical difficulties and requirements faced by the industry
Ceramic powder formula | Metallization process | Assembly adjustment |
---|---|---|
・Less impurities ・Few defects ・Uniform grain distribution |
・Spray uniformity ・Thickness control ・Conductive silver paste quality |
・Structure and homogeneity of finished products |
Supports production inspection
Shimadzu has a variety of characterization and testing systems to study ceramic filter production processes.
Requirements / items in the production process |
Analysis item | Analytical / testing method |
---|---|---|
Uniformity of crystalline powder | Crystal phase identification | X-ray Diffraction(XRD) |
Control and analysis of powder particle size | Particle size distribution measurement | Particle Size Analysis |
Principal component element analysis | Elemental analysis | Wavelength Dispersive X-ray Fluorescence Spectroscopy(WDXRF) |
Trace element analysis, trace/impurity analysis | Inductively Coupled Plasma Emission Spectroscopy / Atomic Absorption Spectroscopy(ICP/AA) | |
Thermodynamic analysis of the effect of additives on the structure of synthetic powders | Thermal analysis | Thermal Analysis(TA) |
Bending test of piezoelectric ceramic material | Mechanical performance evaluation | Bending Testing |
Hardness test of piezoelectric ceramic material | Hardness Testing | |
Observation of gaps, cracks and pores in the ceramic member and on the surface of the finished metal plated layer | Internal structure analysis | X-ray CT |
Application
One of the current problems facing manufacturers is that the electrical performance of the finished product does not meet specified requirements. Many of these problems are caused by the uneven surface of sintered and metallized ceramic parts, as well as the presence of impurities and voids. The Shimadzu X-ray CT system easily identifies impurities and defects in ceramic filters.
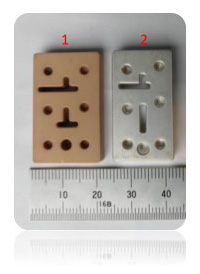
No.1: Ceramic filter
No.2: Ceramic filter with metallization processing
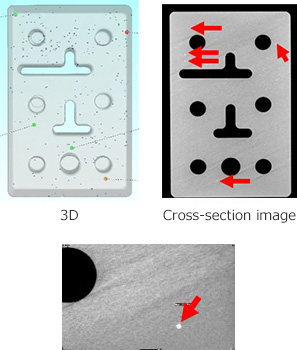
No.1 sample
(White spot: contamination)
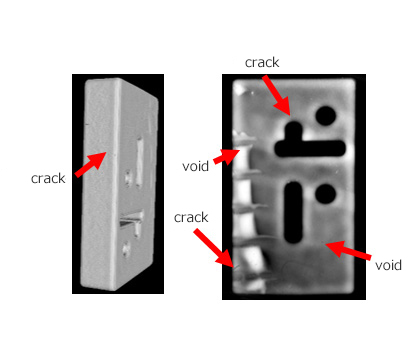
No.2 sample
Testing methods in the research and production of conductive silver paste in the metallization step
To ensure the uniformity of the conductive silver paste required during the metallization process, the formulation, preparation process and manufacture of the silver paste must be studied and controlled.
Control item | Testing requirements | Testing method |
---|---|---|
Physical control of product quality | Solid content | Drying-weighing |
Viscosity | Rotational viscosity method | |
Metal powders such as Ag/Al/Cu | Impurity element analysis | Inductively Coupled Plasma (ICP) Emission Spectroscopy |
Particle size distribution(<500 nm) | Particle Size Analysis | |
Binders such as glass powder | Influence of Vitrification Temperature and Thermogravimetric Curve of Glass Powder on Conductivity Performance of Electron Slurry | Thermal Analysis |
Crystallinity of binder | X-ray Diffraction (XRD) | |
Principal component elemental analysis of glass powder | Energy Dispersive X-ray Spectroscopy | |
Particle size distribution (1 -10 μm) | Particle Size Analysis | |
Organic carrier | Test for solvent purity and other low boiling point organic additives | Gas Chromatography(GC-FID) |
Improvement of Formulation Technology - Study of Action Mechanism | Study on sintering mechanism of functional filler and binder | X-ray Photoelectron Spectroscopy(XPS) |
UV-VIS Spectroscopy | ||
Fourier Transform Infrared (FTIR) spectrometer |